ASTM A387 molybdenum welding/ threaded/carbide rod suppliers in mumbai, China
ASME SA387 Molybdenum Round Bar Manufacturer in China
ASTM A387 is a specification that caters to applications that require elevated temperatures. Particularly, the Molybdenum Rod is a resource in the manufacture of both welded broilers and pressure vessels, due to its chemistry. This specification covers several chromium-molybdenum alloy steel components like rods and bars. Manufacturers can use any one of the following grades as a material to produce a Molybdenum Round Bar, like – grade 2, grade 12, grade 11, grade 22, grade 22L, grade 21, grade 21L, grade 5, grade 9, and grade 91.
This specification demands that the steel used is to be killed as well as thermally treated. The main characteristic of killed steel is that it is completely deoxidized. Since the material for an ASME SA387 Molybdenum Threaded Rod is devoid of any oxygen, there is no progression of gas during solidification. This in turn ensures that the rod is not porous or structurally weak. The steel bars and rods are required to undergo heat analysis and product analysis.
The different elements used to alloy the ASTM A387 Molybdenum Welding Rod must conform to the chemical conditions as mentioned in the specification. Lastly, all components that fall under this specification are required to undergo certain tests. For instance, a tension test is conducted on the rod and the values obtained with regards to properties like tensile strength, yield strength, and elongation must meet the specification.
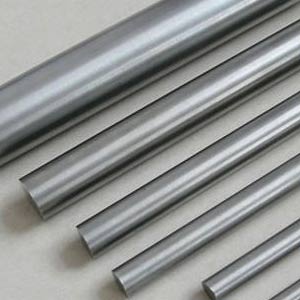
Molybdenum Rod
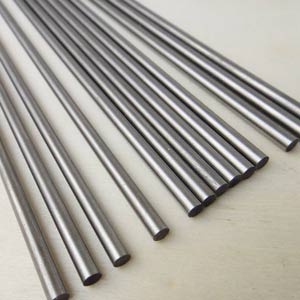
ASTM A387 Molybdenum Round Bar
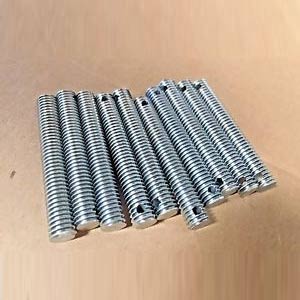
ASME SA387 Molybdenum Threaded Rod
- Standard : ASTM B387
- Material : Mo >99.95%
- Density : 9.8 ~ 10.2g/cc
Molecular Weight
|
95.94
|
---|---|
Appearance
|
Silvery
|
Melting Point
|
2623 °C
|
Boiling Point
|
4639 °C
|
Density
|
10280 kg/m3
|
Solubility in H2O
|
N/A
|
Electrical Resistivity
|
5.2 microhm-cm @ 0 °C
|
Electronegativity
|
1.9 Paulings
|
Heat of Fusion
|
6.6 Cal/gm mole
|
Heat of Vaporization
|
128 K-Cal/gm atom at 4612 °C
|
Poisson’s Ratio
|
0.31
|
Specific Heat
|
0.0599 Cal/g/K @ 25 °C
|
Tensile Strength
|
N/A
|
Thermal Conductivity
|
1.38 W/cm/K @ 298.2 K
|
Thermal Expansion
|
(25 °C) 4.8 µm·m-1·K-1
|
Vickers Hardness
|
1530 MPa
|
Young’s Modulus
|
329 GPa
|
ASTM A387 Alloy Steel Round Bars Manufacturer
CZ121 | CW614N | CuZn39PB3 |
BS2874 | BS249 | – |
MO007900
|
Diameter:6.0mm, Purity:99.9%, Condition:Centreless ground
|
MO007901
|
Diameter:3.0mm, Purity:99.9%, Condition:Centreless ground
|
MO007902
|
Diameter:1.5mm, Purity:99.9%, Condition:Centreless ground
|
MO007903
|
Diameter:2.0mm, Purity:99.9%, Condition:Centreless ground
|
|
|
MO007904
|
Diameter:4.0mm, Purity:99.9%, Condition:Centreless ground
|
MO007905
|
Diameter:5.0mm, Purity:99.9%, Condition:Centreless ground
|
MO007906
|
Diameter:5.0mm, Purity:99.98%
|
MO007907
|
Diameter:3.5mm, Purity:99.9%, Condition:Centreless ground
|
MO007908
|
Diameter:1.25mm, Purity:99.9%, Condition:Centreless ground
|
|
|
MO007910
|
Diameter:8.0mm, Purity:99.9%, Condition:Centreless ground
|
MO007920
|
Diameter:10.0mm, Purity:99.9%, Condition:Centreless ground
|
MO007922
|
Diameter:12mm, Purity:99.9%, Condition:Centreless ground
|
MO007926
|
Diameter:15.0mm, Purity:99.9%, Condition:Centreless ground
|
MO007931
|
Diameter:20.0mm, Purity:99.9%, Condition:Centreless ground
|
MO007945
|
Diameter:25mm, Purity:99.9%, Condition:Centreless ground
|
MO007950
|
Diameter:30mm, Purity:99.9%, Condition:Centreless ground
|
MO007960
|
Diameter:50mm, Purity:99.9%, Condition:Centreless ground
|
MO007975
|
Diameter:75mm, Purity:99.9%, Condition:Centreless ground
|
MO007995
|
Diameter:100mm, Purity:99.9%, Condition:Centreless ground
|
Grade |
The impurity content is not more than % |
|||||||
Fe |
Ni |
Al |
Si |
Mg |
C |
N |
O |
|
Mo-1 |
0.01 |
0.005 |
0.002 |
0.01 |
0.005 |
0.01 |
0.003 |
0.008 |
Mo-2 |
0.01 |
0.005 |
0.005 |
0.01 |
0.005 |
0.01 |
0.003 |
0.02 |
Properties
|
Metric
|
Imperial
|
---|---|---|
Tensile strength (annealed)
|
324 MPa
|
47000 psi
|
Shear strength (torsional strain rate 0.25/s)
|
500 MPa
|
72500 psi
|
Compressive yield strength (0.01% yield)
|
400 MPa
|
58000 psi
|
Modulus of elasticity
|
330 GPa
|
47900 ksi
|
Modulus of elasticity at elevated temperature (@2000°C/3630°F)
|
160 GPa
|
23200 ksi
|
Poissons ratio (calculated)
|
0.38
|
0.38
|
Hardness, Brinell (converted from Vickers for 3000 kg load/10 mm ball Brinell test. annealed)
|
225
|
225
|
Hardness, Rockwell A (converted from Vickers. annealed)
|
60
|
60
|
Hardness, Rockwell B (converted from Vickers. annealed)
|
98
|
98
|
Hardness, Rockwell C (converted from Vickers. annealed)
|
19
|
19
|
Hardness, Vickers (annealed)
|
230
|
230
|
Properties
|
Metric
|
Imperial
|
---|---|---|
Density
|
10.3 g/cm³
|
0.369 lb/in³
|
Melting point
|
2625°C
|
4760°F
|
Properties
|
Metric
|
Imperial
|
---|---|---|
Thermal expansion coefficient (@20°C/68°F)
|
5.35 µm/m°C
|
2.97 µin/in°F
|
Thermal conductivity
|
138 W/mK
|
958 BTU in/hr.ft².°F
|
Diameter[mm]
|
Length[mm]
|
Quality
|
Weight[kg]
|
---|---|---|---|
2.000
|
500 – 3.000
|
ground
|
0.032
|
3.00
|
500 – 3.000
|
ground
|
0.072
|
3.175
|
500 – 3.000
|
ground
|
0.081
|
4.000
|
500 – 3.000
|
ground
|
0.128
|
4.750
|
500 – 3.000
|
ground
|
0.181
|
5.000
|
500 – 3.000
|
ground
|
0.200
|
6.000
|
500 – 3.000
|
ground
|
0.288
|
6.350
|
500 – 3.000
|
ground
|
0.323
|
7.000
|
500 – 3.000
|
ground
|
0.392
|
7.925
|
500 – 3.000
|
ground
|
0.503
|
8.000
|
500 – 3.000
|
ground
|
0.512
|
9.000
|
500 – 3.000
|
ground
|
0.649
|
9.525
|
500 – 3.000
|
forged
|
0.726
|
9.525
|
500 – 3.000
|
ground
|
0.726
|
10.000
|
500 – 3.000
|
ground
|
0.801
|
12.000
|
500 – 2.000
|
ground
|
1.153
|
12.000
|
500 – 2.500
|
ground
|
1.153
|
12.700
|
500 – 2.000
|
ground
|
1.291
|
12.700
|
500 – 2.000
|
forged
|
1.291
|
13.000
|
500 – 2.000
|
ground
|
1.353
|
41.000
|
500 – 2.000
|
ground
|
1.569
|
15.000
|
500 – 2.000
|
forged
|
1.802
|
15.000
|
500 – 2.000
|
ground
|
1.802
|
15.875
|
500 – 2.000
|
ground
|
2.018
|
16.000
|
500 – 2.000
|
forged
|
2.05
|
18.000
|
500 – 2.000
|
forged
|
2.594
|
19.050
|
500 – 1.700
|
forged
|
2.906
|
19.050
|
500 – 1.700
|
forged
|
2.906
|
19.050
|
500 – 1.700
|
ground
|
3.203
|
20.000
|
500 – 1.700
|
forged
|
3.203
|
22.000
|
500 – 1.700
|
ground
|
3.875
|
22.225
|
500 – 1.800
|
forged
|
3.955
|
25.000
|
500 – 2.000
|
ground
|
5.004
|
25.000
|
500 – 2.000
|
forged
|
5.004
|
25.400
|
500 – 2.000
|
ground
|
5.166
|
25.400
|
500 – 2.400
|
forged
|
5.166
|
30.000
|
500 – 2.000
|
ground
|
7.206
|
30.000
|
500 – 2.000
|
ground
|
7.206
|
33.000
|
500 – 2.400
|
forged
|
8.72
|
35.000
|
500 – 2.000
|
forged
|
9.809
|
38.100
|
500 – 2.000
|
forged
|
11.623
|
40.000
|
500 – 2.600
|
ground
|
12.811
|
45.000
|
500 – 2.200
|
forged
|
16.576
|
50.800
|
500 – 2.800
|
forged
|
20.663
|
55.000
|
500 – 2.300
|
forged
|
24.221
|
60.000
|
500 – 1.800
|
forged
|
28.825
|
63.500
|
500 – 3.000
|
forged
|
32.286
|
70.000
|
500 – 1.800
|
forged
|
39.234
|
80.000
|
500 – 3.000
|
forged
|
51.245
|
90.000
|
500 – 2.700
|
forged
|
64.857
|
100.000
|
500 – 2.200
|
smooth forged
|
80.07
|
120.000
|
500 – 2.000
|
smooth forged
|
115.301
|
120.000
|
500 – 2.000
|
smooth forged
|
115.301
|
140.000
|
300 – 500
|
smooth forged
|
156.937
|
165.000
|
300 – 500
|
extruded
|
217.991
|
Diameter[mm]
|
Length[mm]
|
Quality
|
Weight[kg]
|
---|---|---|---|
4.750
|
500 – 3.000
|
ground
|
0.181
|
6.000
|
500 – 3.000
|
ground
|
0.288
|
6.350
|
500 – 3.000
|
ground
|
0.323
|
8.000
|
500 – 3.000
|
ground
|
0.512
|
10.000
|
500 – 3.000
|
ground
|
0.801
|
12.700
|
500 – 2.000
|
forged
|
1.291
|
15.875
|
500 – 2.000
|
ground
|
2.018
|
16.000
|
500 – 1.600
|
forged
|
2.05
|
18.000
|
500 – 2.000
|
forged
|
2.594
|
19.050
|
500 – 1.500
|
ground
|
2.906
|
20.000
|
500 – 2.000
|
forged
|
3.203
|
22.225
|
500 – 2.000
|
forged
|
3.955
|
25.000
|
500 – 2.000
|
forged
|
5.004
|
25.400
|
500 – 1.900
|
forged
|
5.166
|
26.670
|
500 – 1.800
|
forged
|
5.695
|
30.000
|
500 – 1.600
|
forged
|
7.206
|
31.750
|
500 – 1.400
|
forged
|
8.072
|
33.000
|
500 – 1.400
|
forged
|
8.72
|
35.000
|
500 – 2.000
|
forged
|
9.809
|
40.000
|
500 – 3.000
|
forged
|
12.811
|
45.000
|
500 – 2.000
|
forged
|
16.214
|
49.500
|
500 – 1.600
|
forged
|
19.619
|
55.000
|
500 – 1.800
|
forged
|
24.221
|
63.500
|
500 – 2.800
|
forged
|
2.05
|
70.000
|
500 – 1.800
|
forged
|
2.594
|
80.000
|
500 – 2.500
|
forged
|
2.906
|
90.000
|
500 – 2.300
|
forged
|
2.906
|
100.000
|
500 – 3.000
|
forged
|
3.203
|
140.000
|
300 – 500
|
forged
|
3.203
|
165.000
|
300 – 500
|
forged
|
3.875
|
- Used in electric vacuum parts, steel-making additives, gas pipes, sidebar, lead-wire, optical glass, daily-use glass, glass fiber and insulation material
- Used to stretch into molybdenum electrode and molybdenum wire
Diameter
|
Black/Clean
|
Ground
|
.020 to .025
|
± .001
|
± .001
|
.025 to .070
|
± .0015
|
± .001
|
.070 to .200
|
± .002
|
± .001
|
.200 to .250
|
± .007
|
± .001
|
.250 to .437
|
± .007
|
± .0015
|
.437 to .750
|
± .010
|
± .003
|
.750 to 1.000
|
± .015
|
± .005
|
1.000 to 1.250
|
± .015
|
± .005
|
1.250 to 1.750
|
± .025
|
± .005
|
Diameter
|
.5″ to 12″
|
12″ to 24″
|
> 24″
|
.020 to .100
|
± .010
|
± .015
|
± .0625
|
.100 – .500
|
± .015
|
± .015
|
± .0625
|
.500 to 1.000
|
± .015
|
± .030
|
± .0625
|
1.000 to 1.500
|
± .030
|
± .0625
|
± .0625
|