BeCu round bar and Casting Manufacturers.
chromium and beryllium Copper Hex, Flat and Square Bar Suppliers
There are multiple reasons for alloying beryllium with copper and chromium alloys. The Beryllium Chromium Copper Rod exhibits a host of impressive properties including good hardness, and elasticity, with higher electrical conductivity as well as higher thermal conductivity. The alloy has a high melting point, and hence, the Chromium And Beryllium Copper Hex bar could be used for applications that require high temperatures.
The initial use of these alloys was in the field of defense and as components in the aerospace industries. Beryllium in minute quantities also improves the tensile strength of the copper, making it far stronger than plain copper itself. In addition to having high tensile strength and good hardness, the Beryllium Chromium Copper Flat bar exhibits nonmagnetic properties, as well.
Therefore, the alloy is well suited for use in applications that do not require any degree of magnetism. A higher percentage of copper with significant amounts of chromium and beryllium improve properties such as resistance to corrosion and fatigue resistance in the BeCu Square Bar. Another important property of this alloy is its exceptional ability to dissipate heat, which was the sole reason for the use of a BeCu Round Bar in brakes for military airplanes.
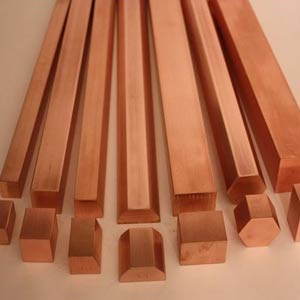
Beryllium Chromium Copper Rod
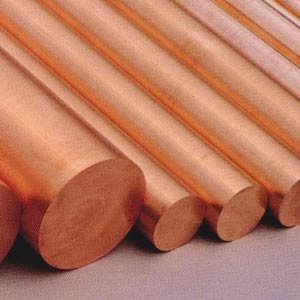
BeCu round bar
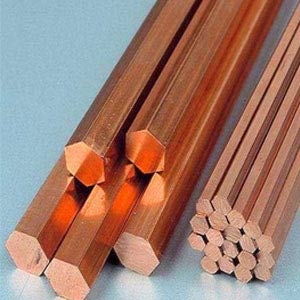
Chromium And Beryllium Copper hex bar
Standard & Material
|
CDA 110 ETP, ASTM B124, ASTM B152, ASTM B187, ASTM B188, ASTM B272
|
HOLLOW RODS
|
Min Bore Size 20 mm and Max OD 100 mm
|
ROUND RODS
|
8mm To 100 mm
|
HEX
|
10mm To 60mm
|
SQUARE
|
10mm To 60mm
|
FLAT
|
10mm Min Thickness and max Width 120mm
|
BILLETS
|
Up to 200 mm
|
INGOTS
|
As per Specification
|
- Architectural Industry
- Antimicrobial Applications
- Electrical Industry
- Telecommunications Industry
End Product
|
Specification
|
Bar
|
ASME SB133, ASTM B152, SAE J461, J463
|
Bar, Bus
|
ASTM B187
|
Bar, Forging
|
ASTM B124
|
Rod
|
ASME SB133, MILITARY MIL-C-12166, SAE J461, J463
|
Rod, Bus
|
ASTM B187
|
|
Cu
|
O
|
Min/Max
|
99.90 min
|
|
Nominals
|
–
|
0.04
|
Product Property
|
US Customary
|
Metric
|
Coefficient of Thermal Expansion
|
9.4 · 10 6? per °F (68-212 F)
|
16.9 · 10 6? per °C (20-100 C)
|
Coefficient of Thermal Expansion
|
9.6 · 10 6? per °F (68-392 F)
|
17.3 · 10 6? per °C (20-200 C)
|
Coefficient of Thermal Expansion
|
9.8 · 10 6? per °F (68-572 F)
|
17.6 · 10 6? per °C (20-300 C)
|
Density
|
0.322 lb/in3 @ 68 F
|
8.91 gm/cm3 @ 20 C
|
Electrical Conductivity
|
101%IACS @ 68 F
|
0.591 MegaSiemens/cm @ 20 C
|
Electrical Resistivity
|
10.3 ohms-cmil/ft @ 68 F
|
1.71 microhm-cm @ 20 C
|
Melting Point Liquid US
|
1981 F
|
1083 C
|
Melting Point Solid US
|
1949 F
|
1065 C
|
Modulas of Elasticity in Tension
|
17000 ksi
|
117000 MPa
|
Modulas of Rigidity
|
6400 ksi
|
44130 MPa
|
Specific Gravity
|
8.91
|
8.91
|
Specific Heat Capacity
|
0.092 Btu/lb/ °F at 68 F
|
393.5 J/kg · °K at 293 K
|
Thermal Conductivity
|
226.0 Btu · ft/(hr · Ft2 · °F) at 68 F
|
391.1W/m · °K at 20 C
|
Joining Technique
|
Suitability
|
Brazing
|
Good
|
Butt Weld
|
Good
|
Capacity for Being Cold Worked
|
Excellent
|
Capacity for Being Hot Formed
|
Excellent
|
Coated Metal Arc Welding
|
Not Recommended
|
Forgeability Rating
|
65
|
Gas Sheilded Arc Welding
|
Fair
|
Machinability rating
|
20
|
Oxyacetylene Welding
|
Not Recommended
|
Seam Weld
|
Not Recommended
|
Soldering
|
Excellent
|
Spot Weld
|
Not Recommended
|